The history of safety glass
By Kiron Kasbekar | 26 Mar 2025
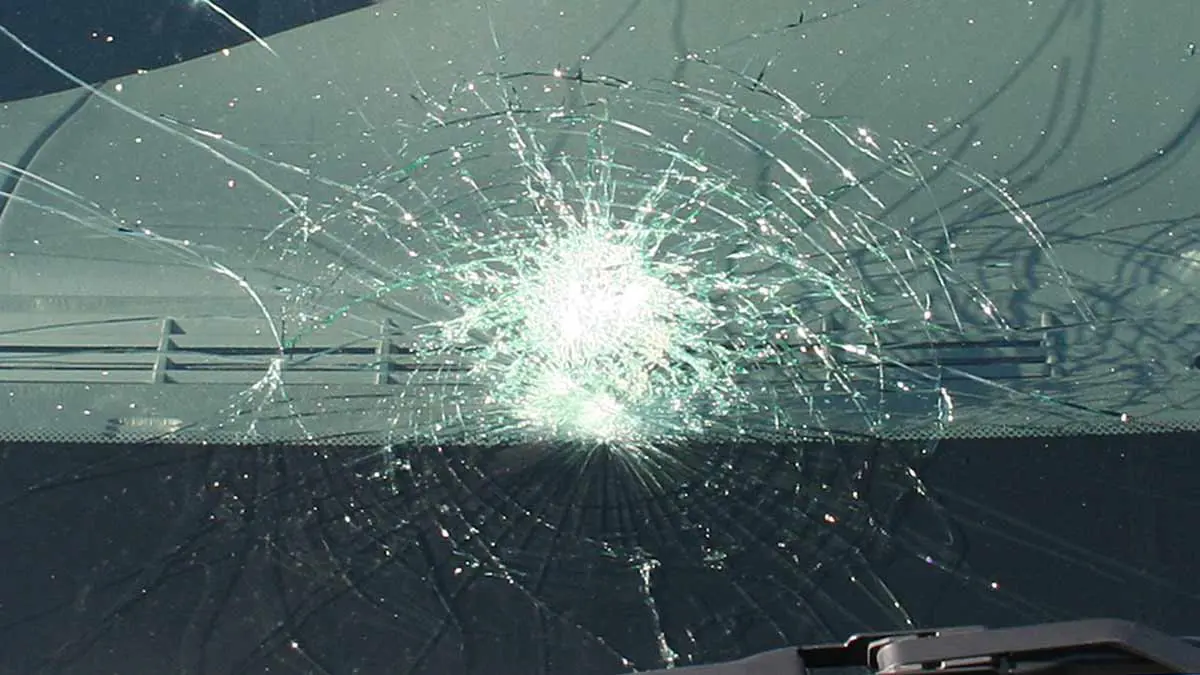
You probably already knew that the world’s VIPs move around in cars with bullet-proof glass windscreen and windows. But did you know that ‘bulletproof glass’ is not really bulletproof? If you wish to be accurate, you can only call it ‘bullet-resistant’ glass.
Whatever you call it, such glass represents one of the most significant safety innovations of modern times. It has saved lives and revolutionized security across various sectors, from banking and government to personal transportation and military applications.
Bulletproof glass is just one of the types of safety glass.
Édouard Bénédictus
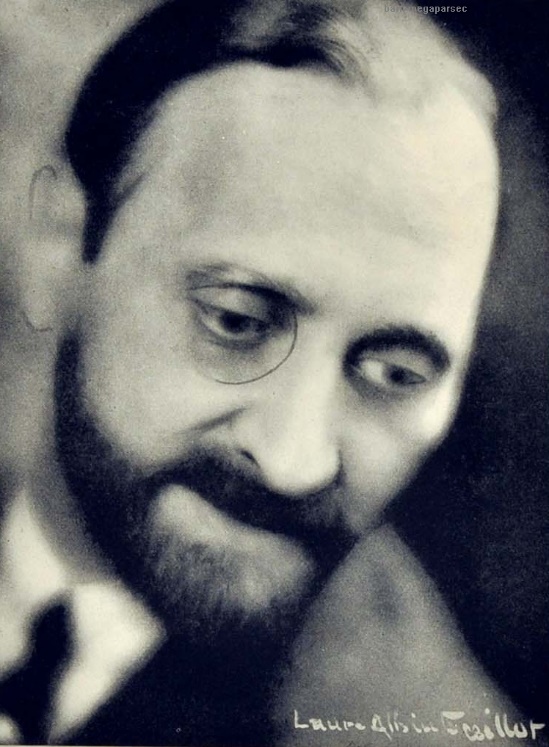
There is some mention of a patent being obtained in 1902 by Le Carbone of France for coating glass objects with celluloid so as to render them less susceptible to cracking or breaking. But historical sources almost unanimously give the credit of the invention of safety glass to French chemist Édouard Bénédictus.
So the story of safety glass begins when Bénédictus accidentally discovered the basic principle behind laminated glass in 1903.
One day, when he was working in his laboratory in Paris, he dropped a glass flask that had contained cellulose nitrate. He noticed that while the glass shattered, the fragments remained bonded to the dried chemical film inside, preventing the flask from breaking apart.
That accident triggered a thought in Bénédictus’s mind. After assimilating what had happened, and after working out various product possibilities, he filed a patent in 1909. That patent was for what he called ‘Triplex’, the first commercially viable laminated glass.
Bénédictus’s invention consisted of two glass sheets with a celluloid interlayer, which held the glass together upon impact. Remember, celluloid itself had been invented barely a half century earlier; so it’s no surprise that such a glass sandwich had not been conceived of earlier.
Curiously, Bénédictus is known more for his paintings than for his invention of laminated glass.
Safer glass
Glass is generally a material that has to be handled with the utmost care.
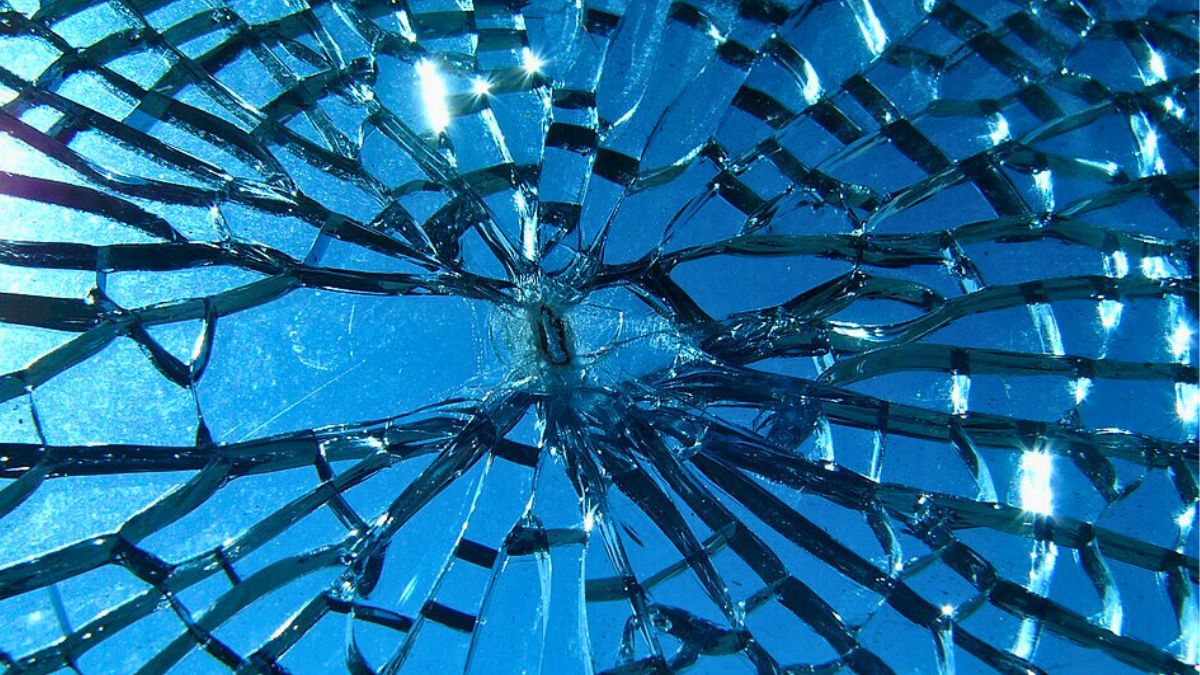
A glass object falling to the ground has a very high probability of shattering and scattering sharp shards that can cause considerable injury to people nearby, and even people who come across it afterwards, stepping on or picking up sharp glass pieces.
Fortunately there are many types of glass that have been rendered safer than they used to be. Most flat glass today can be strengthened to withstand hard impacts.
I say “can” because glass is not always strengthened.
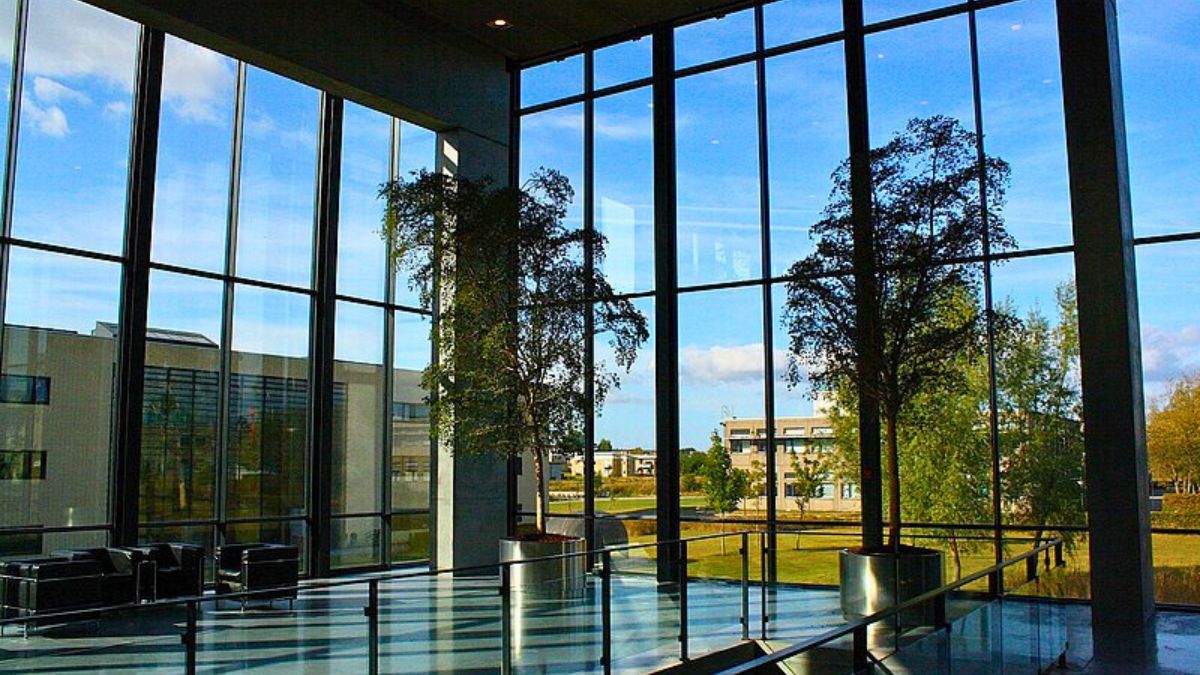
If you want strengthened glass you need to first cut the glass sheets in the required shapes and sizes and then get the cut pieces tempered. Why? Because once a glass sheet is tempered, it cannot be cut. An attempt to cut it will result in the sheet crumbling into small pieces.
It is a good idea to strengthen glass used in windows and partitions.
There was one occasion when a carpenter working in my office accidentally smashed a partition glass panel as he swung a wooden beam he was carrying on his shoulder. The glass simply disintegrated into small pieces, none of them sharp.
Nobody was hurt. I had ordered several spare panels in advance; so we simply had to pull one out of the store and replace the shattered pane.
Strenthened
Toughened glass does not break easily, but if it does break, it disintegrates into a multitude of small pieces that have no sharp edges.
You may have noticed that when a car windshield breaks, it does not break up into sharp, angular pieces, but into small granular chunks. That’s because car windshields and windows are made of toughened glass.
Use of such glass prevents the panes from shattering and hurting people or pets. For many years now I have had the glass in my windows and doors strengthened. In my office and at home.
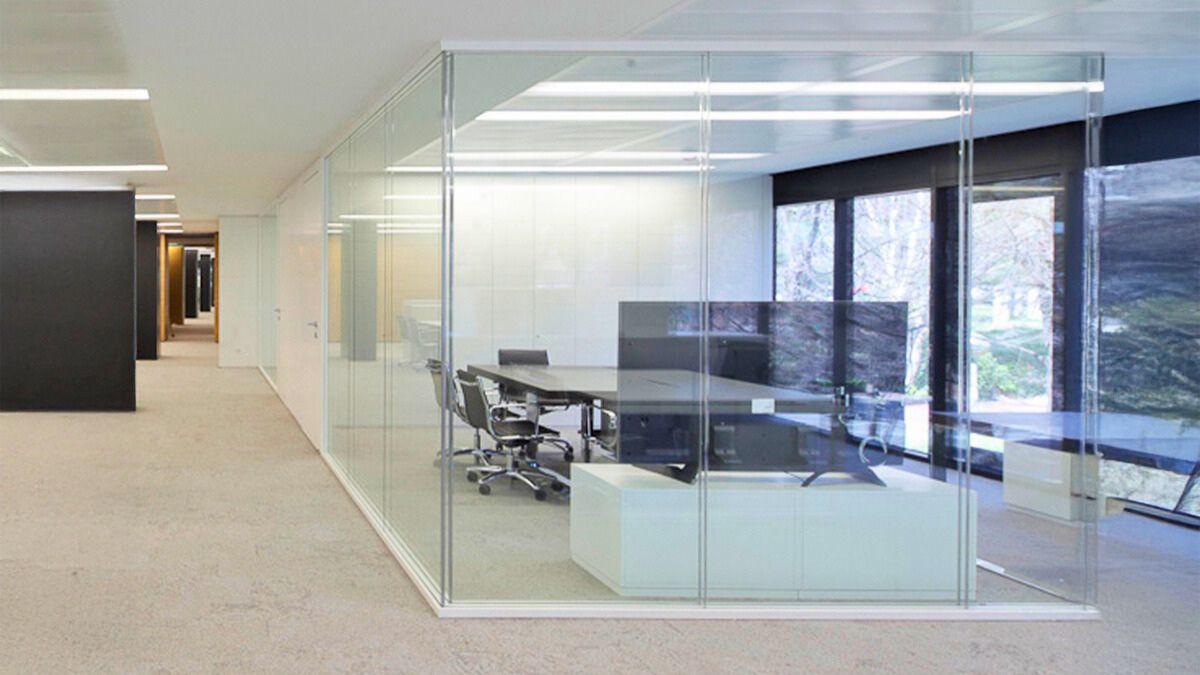
But many people in India and other countries do not bother to use toughened glass for windows and doors. One of the reasons is not knowing about safety glass. Another reason is cost; safety glass is more expensive. Sometimes people suffer because of this lapse.
Now, since the beginning of the 21st century, we have a variety of safety glass available.
Places like America, some European countries, and Japan stand out for their safety regulations on glass usage. Japan, because of its geological vulnerabilities, has stringent seismic performance requirements.
Generally windshields of automotive vehicles are now required to be made of laminated safety glass. Side and rear windows may be made of laminated glass or tempered glass.
Safety glass is also required to be used in public buildings
The International Building Code (IBC) requires the use of tempered or laminated glass in doors, shower enclosures, stairs and railings, and areas with high human impact risk. Fire-rated glass in critical building locations, and specific safety ratings have been laid down for hurricane-prone regions.
Today’s smartphones and tablets require their screen covers to be very durable. So they do not shatter if they fall to the floor or are flung against a wall. They are made of chemically strengthened glass. The glass protects the devices.
Corning was first
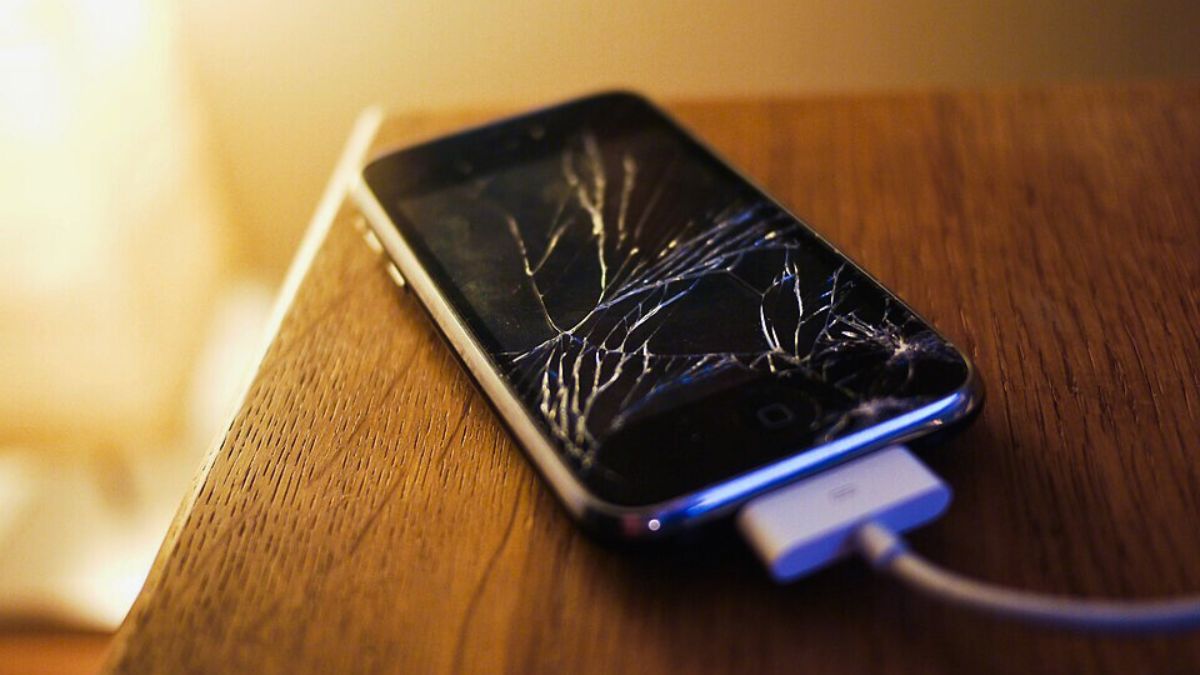
The most visible and most widely used of such glass is used on mobile phones. Corning Inc., the US-based company, was the first to launch such glass. It was quickly followed by others.
You may have heard the term ‘Gorilla Glass’. It is called that because it is very strong, and its use in mobile phones ensures that a high degree of safety. Gorilla Glass is a brand name owned Corning, the American manufacturer of specialty glass, ceramics, and related materials.
Corning introduced Gorilla Glass in 2007. This alkali-aluminosilicate glass is remarkably thin, light and scratch resistant.
The manufacturing process of Gorilla Glass involves what is known as the ion-exchange method, in which the glass is immersed in a molten alkaline potassium salt bath at about 400°C, where smaller sodium ions in the glass are replaced by larger potassium ions. That creates a layer of compressive stress that enhances the glass’s strength and durability.
Corning has released multiple variations of Gorilla Glass, each offering greater durability and resistance to damage. Gorilla Glass 5, launched in 2016, could survive drops from heights of up to 1.6 meters, or five and a quarter feet. Gorilla Glass 6, launched in 2018, offered twice strength.
In 2020, Corning launched Gorilla Glass Victus, which offers enhanced scratch resistance and drop performance. And in November 2022 it launched Gorilla Glass Victus 2, with improved scratch resistance and drop performance on rough surfaces.
But Corning is not the only company making strengthened glass. AGC Inc. (formerly Asahai Glass Company) sells Dragontrail, and Schott AG of Germany sells Xensation. Each of these products offers unique features and has carved out a significant presence in the global market.
AGC’s Dragontrail
Next came Japanese multinational Asahi Glass Company (AGC), which introduced Dragontrail Glass in 2011.
Dragontrail glass is also an alkali-aluminosilicate glass but is manufactured using a ‘chemical float’ process. This method involves floating molten glass over a bed of molten tin, resulting in a flat and uniform sheet. Particles are then added for strengthening before the glass is rapidly cooled and cut to size.
Dragontrail too has gone through several avatars. The original Dragontrail glass, which Asahi Glass claimed was six times stronger than conventional soda-lime glass, was followed by Dragontrail X in 2014. That offered 30 per cent greater strength than its predecessor. Dragontrail Pro, launched in 2016, featured rounded edges to better distribute impact forces, and that made it suitable for high-end, stylish phones with exposed edges.
By 2014, Dragontrail was adopted by some three dozen major electronic device brands worldwide, and sales grew at a rapid clip.
Schott’s Xensation
Schott AG, a German technology enterprise founded in 1884, entered the mobile phone cover glass market in 2012 and launched Xensation. This alumino-silicate glass is yet another break- and scratch-resistant glass.
Schott has developed various versions of Xensation to cater to different device requirements, including Xensation Alpha, Flex, 3D, and Up. For example, Xensation Alpha, released in 2021, is a chemically strengthened lithium alumino borosilicate (LABS) cover glass that first appeared in the Vivo S12 Pro.
Xensation glass has been adopted by several leading smartphone manufacturers, including OnePlus, Vivo, Huawei/Honor, and OPPO. This adoption indicates its growing presence in the market and its competitiveness against established players like Gorilla Glass and Dragontrail.
Comparative analysis
When comparing these glass covers, we need to consider factors like scratch resistance, durability, optical clarity, touch sensitivity, and chemical resistance.
- Scratch resistance: All three glass brands offer very good scratch resistance. However, there are variations depending on the version and manufacturing process. For instance, Gorilla Glass Victus is designed to withstand drops from up to two meters while offering double the scratch resistance of Gorilla Glass 6.
- Durability: Each of these glass brands is engineered to withstand impacts and reduce the risk of display damage from drops.
- Optical clarity and touch sensitivity: All three types of glass are designed to provide clear and vibrant displays with smooth and responsive touch experiences, essential for modern touch-enabled devices.
- Chemical resistance: Improved chemical resistance protects the glass from damage due to exposure to various chemicals, oils, or cleaning agents.
- Market presence and adoption: Gorilla Glass has maintained a dominant position in the market, with a significant presence in the global smartphone industry. Later arrivals Dragontrail and Xensation have secured significant market shares, with numerous device manufacturers incorporating these glasses into their products.
This was just a fleeting glance at a part of the glass industry. But I hope it triggers an interest to know more about the industry.